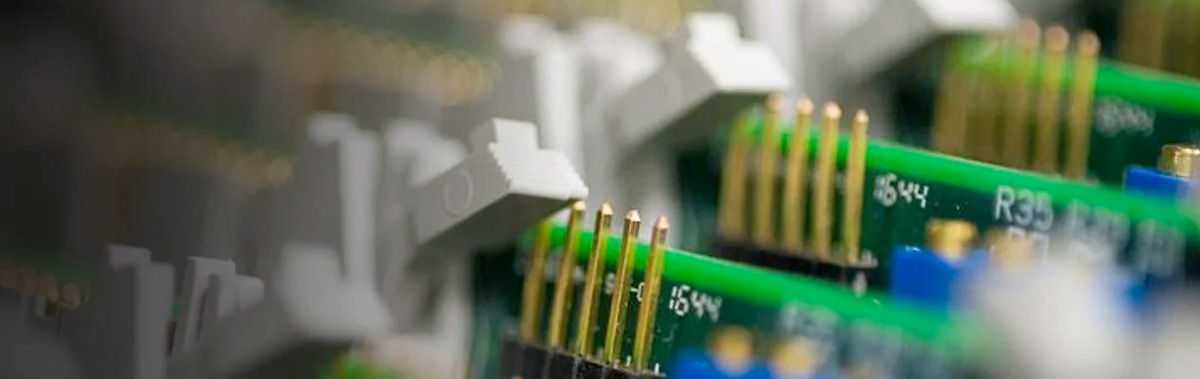
WeldComputer Corporation designs and builds control, monitoring, and adaptive equipment for automated resistance welding in manufacturing environments for a wide variety of industries, from aerospace and defense to medical, automotive, and electronics.
"We offer high-performance, computerized resistance welding methods that reduce defects and improve overall weld quality for high-quality products at lower costs," says founder and CEO Robert Cohen.
Manufacturers that benefit from WeldComputer technologies include jet engine, aircraft, rockets, and space satellite developers; airbag inflators, water heater, and appliance manufacturers; and makers of batteries, wire contacts, and relays in the electronics industry, to name a few.
Established in 1987, WeldComputer was built to tackle the most difficult welding application requirements from the start, partnering with such clients as NASA and the U.S. Department of Defense.
"We made a system for NASA that was put on a hand truck to wheel up to the Space Shuttle launch site to weld the heat shielding on the engine on the morning before liftoff," Cohen says. "They told us if they turn this on and it doesn't work, it would delay the shuttle launch."
WeldComputer has since worked with businesses as varied as those that make garage door openers and refrigerator racks.
"Over the years, more companies have come to realize that bad welds on products cost a lot of money and can present liabilities," Cohen says.
WeldComputer, which specializes in equipment for spot, seam, projection, and flash/butt welding, offers three levels of welding solutions, from basic consistent heat control to the most sophisticated adaptive applications. The company also offers support services to train manufacturing staff how to interpret and apply its equipment data and to identify key sources of weld inconsistencies.
"We provide vision for a process that has been traditionally done blindly," Cohen says. "Our machines provide the ability to know that there's a quality problem without having to do destructive testing, which has been the conventional approach in this industry."
For instance, some companies have spent up to 25 percent of production time destroying samples in the attempt to verify that satisfactory welds are being produced, eating up valuable time and producing costly waste.
WeldComputer can also tailor its equipment to meet special application requirements. For instance, a machine was recently shipped to a company in South Africa that contains a 3 million-watt power supply to run a single resistance welding machine, which is adjusted eight times per millisecond.
"That's equivalent to changing the setting on 2,000 residential space heaters 8,000 times a second," says Cohen.
Cohen, who graduated from Rensselaer Polytechnic Institute with an electrical engineering degree, began to develop the core technology that makes up the foundation of WeldComputer while working as an engineer for what is now GE Global Research. In the end, General Electric did not pursue the technology because of the cost and time to set up such a business venture.
Cohen moved on to further develop the technology in the Troy area. WeldComputer, which has a mix of office, lab, and manufacturing space, has been at the Rensselaer Technology Park Campus since 1994.
"The Technology Park provides a pleasant and comfortable work space, and it's nice to be in a high-tech environment that's free of distraction," Cohen says. "The Technology Park also has been great about meeting our needs for facility expansion as our company has grown over the years."
All WeldComputer products are made in the United States and are available globally.